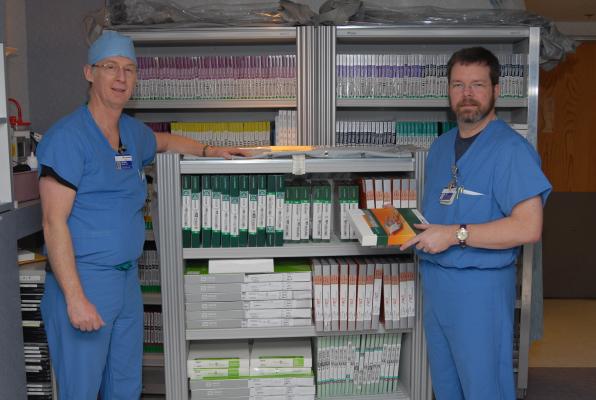
An example of RFID cabinets in a cath lab. As items are pulled from the cabinet, the inventory control system automatically determines what items were taken out and adds them to the patient case. The system can also help locate recalled or expired items, and automatically track on-hand inventory to avoid manual counts.
The healthcare industry’s transition to value-based care leaves no room for waste, and yet we know that inefficiency in the medical devices market alone leads to an estimated $5 billion in waste annually.[1] High-cost, high-value medical devices and implantables such as stents and pacemakers continue to flow through a highly inefficient supply chain.
• Every day, the healthcare supply chain loses inventory to shrinkage and product expiration. In fact, 7-10 percent of products likely expire on hospital shelves.[2]
• Nurses can spend as much as 30 percent of their time searching for products that may or may not be used during a procedure – that is more than two hours per shift per nurse.[3]
• Health systems are losing as much as 1 percent of their potential annual net revenue due to various issues associated with charge capture.[4]
Health systems need new approaches to promoting high quality, cost-effective patient care, and 85 percent of respondents to a national survey of hospital executives said their health systems are currently working to identify or implement new ways to reduce supply chain waste and related costs. A more efficient supply chain can enable hospitals and health systems to reduce product expirations and related patient safety issues, facilitate efficient product recall processes, improve cash flow by reducing excess inventory and improve the charge capture process. Additionally, a more efficient supply chain better equips hospitals to efficiently manage high-value products, freeing up clinical staff from inventory management activities and allowing them to focus on patient care.
To reach that end, partners across the healthcare continuum must create product visibility from the manufacturer to the hospital to the point of use. A shared data platform among hospitals, device manufacturers, and distributors can help solve for this problem by allowing them to see the same data and react to it. The data gleaned from this connectivity can enable proper management of consigned inventory, accurate clinical documentation and product and workflow standardization across entire enterprises. In preparation for bundled payments, another industry transition, systems can understand and manage the true cost of care.
Read the article “Advances in Cardiology Inventory Tracking Systems.”
How Can We Get There?
A collaborative, cloud-based platform enabled by radio frequency identification (RFID) technology provides full visibility for day-to-day inventory management and enables long-term inventory planning. Integrated with electronic medical records and other hospital IT systems, the solution provides for complete interoperability and data and analytics that promote transparency and efficiency in the supply chain. This allows health systems to identify their aggregate spend across care sites and points where they have potential for cost avoidances. A heightened level of visibility allows them to optimize their inventory levels, lower costs, streamline workflows and see new insights to improve performance.
Why RFID?
In an industry with competing priorities, investment in any particular technology can be a challenge. But RFID is positioned to become the gold standard technology in this new era of connected end-to-end visibility. Automated systems can monitor high-value medical devices from the manufacturer all the way to the point of care. Such systems track every item in a hospital from the time it arrives from the supplier to the moment it is implanted in a patient or disposed of. With RFID, inventory can be accounted for via near real-time updates from data captured automatically and accurately, and supplies can be reordered automatically. Likewise, the technology enables alerts about expired, soon-to-expire or recalled items.
RFID-tagged products can be housed in a "smart" supply cabinet. Inventory tracking software notes when a supply is removed from the cabinet without the need for manual entry. The item is then scanned in the operating room and linked to a particular patient, helping to improve the charge capture process. If the item is not used, it is automatically placed back into inventory and removed from the patient record when it is returned to the cabinet.
RFID tagging and RFID smart cabinets ensure the critical information needed to track high-value medical devices and implantables automatically displays in the hospital's inventory profile. This includes the model number, serial number, lot number, expiration date, cost and purchase order. RFID smart cabinets can perform inventory counts as often as necessary, to near perfect accuracy, without any potential for human error. And, the cabinet sends automatic alerts when products are removed, expired, recalled or out of stock.
Scalability for success
Many supply chain decision makers have better success starting with a technology deployment on a smaller scale, in a single department such as a cath lab, for example, to demonstrate the return on investment. Then building on that foundation, it can be expanded into other procedural areas and to the operating room (OR). In these cases, though, it is essential to consider scalability and future-proofing at the outset. Otherwise, health systems could end up overhauling all the initial work down the road.
This is a key reason RFID is set to take the stage as the gold standard for inventory management technology. Barcoding may work well for inexpensive products, but the physical effort required to scan each item along with the associated, error-prone processes can hamper efficiency gains on a larger scale for high value medical devices. RFID, on the other hand, can capture far more data than barcodes in an extensively automated system.
Additionally, because these connected technologies are increasingly cloud-based, they provide the opportunity to aggregate data. This means that providers can compare their own metrics — inventory turns, cost per procedure, etc. — to metrics from facilities across their IDN. And in doing so, they can identify areas where they can improve, as well as strategies for getting there.
In an environment where healthcare providers are being challenged to deliver higher quality care to an increasing number of patients more cost effectively than ever before, advanced inventory management technology is the foundation upon which healthcare manufacturers and providers can build a data-enabled, connected supply chain based on real-time data capture. The healthcare supply chain is a strategic asset that can drive out waste and yield large financial savings — especially when it comes to high-value medical devices. The efficiency and savings gains from this connected supply chain promise to meet increased demands to reduce operating costs and free up resources for supporting improved “service at the bedside” and patient satisfaction.
Watch the video “Inventory Management – A Way to Curb Medical Device Waste.”
Inventory Management Systems Comparison Chart
DAIC has compiled vendor specifications for several inventory management systems marketed for cath labs and surgical ORs. The Inventory Management Chart can be found at www.dicardiology.com/content/inventory-management. Access to the chart details will require a login, but it is free and only takes a minute.
Editor’s note: The author Jean-Claude Saghbini is a nationally renowned expert on RFID and SaaS, and holds four patents and six patent-pending applications. He is the chief technology officer and vice president of inventory management solutions at Cardinal Health.
References:
1. PNC Healthcare; GHX quantitative research study (August 2011).
2. Modern Healthcare. “Losing Preferential Treatment.” February 2013
3. Intelligent Insites. “Curing Operational Inefficiency.” 2010.
4. Modern Healthcare. “Charging for Services Provided is Not as Automatic is It Might Seem.” August 2016.
5. Cardinal Health Survey Data; Data on file (2015)